
Stearyl Methacrylate synthesis
- Product Name:Stearyl Methacrylate
- CAS Number:32360-05-7
- Molecular formula:C22H42O2
- Molecular Weight:338.57

112-89-0

920-46-7

32360-05-7
1) 20.0 g of stearyl bromide (octadecyl bromide) was added to a 1000 mL single-necked flask with 250 mL of methylene chloride and 17.7 g of triethylamine, and 16.65 g of methacryloyl chloride was slowly added dropwise under stirring conditions. After the dropwise addition, the reaction was continued with stirring for 5 hours. Upon completion of the reaction, the reaction mixture was washed sequentially with water, saturated sodium carbonate solution and saturated sodium chloride solution. The organic phase was separated, dried with anhydrous sodium sulfate, concentrated under reduced pressure, and finally purified by column chromatography to afford 18.4 g of octadecyl 2-methyl-2-propenoate in 76% yield.

112-92-5
500 suppliers
$5.00/10g

80-62-6
626 suppliers
$19.00/25mL

32360-05-7
317 suppliers
$19.00/10g
Yield:32360-05-7 99.3 %Chromat.
Reaction Conditions:
Stage #1: 1-octadecanol;methacrylic acid methyl esterwith 4-acetylamino-2,2,6,6-tetramethyl-1-piperidinoxy for 1 h;Heating / reflux;
Stage #2: titanium tetramethoxide at 111 - 129; for 4 h;Product distribution / selectivity;
Steps:
2
Example 2; The same reaction apparatus as used in Example 1 was used. First, the reactor was charged with 750.9 9 (7.5 mol) of methyl methacrylate, 676.3 g (2.5 mol) of stearyl alcohol and 0.042 g of 4-acetylamino-2,2,6,6-tetramethylpiperidine-N-oxyl, and the mixture was then heated to conduct dehydration in the reaction system over a period of 1 hour under the total reflux. Then, the reactor was cooled and charged with 1.23 g (0.005 mol) of tetramethyl titanate (purity: 70%), and heating was begun again. And thereafter, the ester-exchange reaction was carried out in the same manner as in Example 1. At the beginning of the reaction, the operation was conducted under the total reflux, and the removal of an azeotropic mixture of methanol/methyl methacrylate from the reaction system was started at the time when the temperature of the uppermost stage in the distillation column reached 64.5° C., the temperature of the middle stage 74° C., and the temperature of the lowest stage 98.8° C. (the conversion of 4% at this time). Thereafter, until the conversion reached 97%, the reaction was carried out while controlling the reflux ratio within the range of 5 to 50, so as to maintain the temperature of the uppermost stage in the distillation column at 64 to 65° C., the temperature of the middle stage at 70 to 80° C., and the temperature of the lowest stage at 99 to 100° C. After 4 hours from the beginning of the reaction, the conversion reached 98% and the temperature of the middle stage in the distillation column rose to 93° C. Thereafter, in order to completely remove, from the reaction system, methanol contained in the liquid refluxed from the uppermost stage in the distillation column to the uppermost stage in the distillation column again through the condenser and the reflux line, the reflux ratio was set to zero, and thereby all the liquid in the reflux line was distilled off until the temperature of the uppermost stage in the distillation column was stably maintained at 98° C. or higher. Thus, the reaction was terminated. The reaction time was 4.5 hours. During this time, the temperature of the uppermost stage in the distillation column was maintained at 95° C. or higher, and the temperatures of the middle stage and the lowest stage in the distillation column were maintained at 99° C. or higher. The amount of the azeotropic mixture of methanol/methyl methacrylate removed was 124.5 g, and the content of methanol was 62.8% (78.2 g) and the content of methyl methacrylate was 37.2% (46.3 g). When 1297.7 g of the resulting reaction solution in the reactor was analyzed by gas chromatography, it contained 35.0% of methyl methacrylate, 0% of stearyl alcohol and 64.8% of stearyl methacrylate, and the yield was 99.3%.
References:
US2006/84823,2006,A1 Location in patent:Page/Page column 5-6

112-92-5
500 suppliers
$5.00/10g
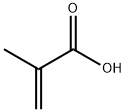
79-41-4
533 suppliers
$14.00/5g

32360-05-7
317 suppliers
$19.00/10g

112-89-0
368 suppliers
$5.00/25g

920-46-7
342 suppliers
$20.00/1g

32360-05-7
317 suppliers
$19.00/10g

112-92-5
500 suppliers
$5.00/10g

920-46-7
342 suppliers
$20.00/1g

32360-05-7
317 suppliers
$19.00/10g